- News & Insights
- 2022
- Optimize your supply chain with safe and sustainable LiB packaging
- Lithium Batteries
- Industries
NEWS & INSIGHTS
Safe and sustainable LiB packaging
Optimize your supply chain with safe and sustainable LiB packaging
Climate change has never been such an urgent matter. As the world seeks to switch from fossil fuel power to emissions-free electricity, Lithium-ion Batteries (LiBs) are emerging as a vital storage tool in this challenging energy transition.
Despite the COVID-19 outbreak and global supply chain disruptions, the LiB market is one of the fastest developing industries. The growing demand is driven mostly by the increased need for electric vehicles (EVs), energy storage systems (ESS), portable electronics, and tools. In fact, the latest predictions say that by 2030, the global market need for LiBs will grow 17 times, reaching an unimaginable 9,300 GWh. To put it in perspective, this accounts for tens of millions of batteries for electric cars, storage containers, and consumer devices around the world.
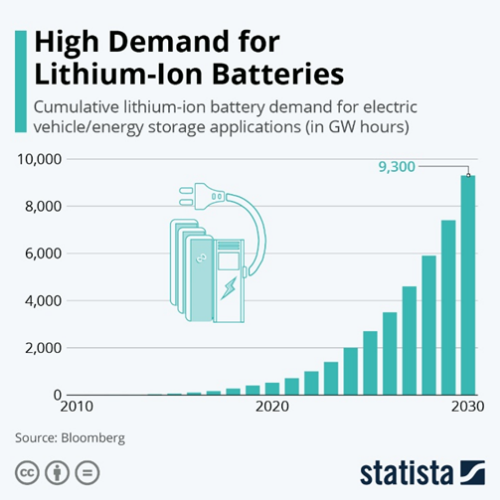
According to Bloomberg, the global market demand for LiBs will grow nearly 17 times by 2030 and reach 9,300 GWh (Statista).
The industry has been debating how to meet this enormous demand for quite some time. Keeping in mind how dangerous it is to transport such large numbers of batteries across different regions due to their highly flammable nature, it was imperative to establish a complete domestic battery chain in Europe. According to the experts, the European firms already have the capacity to supply all LiBs needed for the regional automakers by 2025, as they ramp up the electric vehicle output to meet strict pollution limits. They are expected to produce between seven and eight million batteries which are more than the current needs of domestic EV manufacturers. In fact, the European Battery Alliance is spending €20 billion to support the building of 70 cell factory projects in 12 EU member states.
Given the growing market demand, there is an urge for safe and sustainable packaging solutions to optimize the transportation costs of LiBs. Follow along as the three key challenges that the LiB packaging must overcome to meet these demands are revealed.
Meeting the requirements for LiB transportation
The switch from traditional energy supply to LiBs is a true revolution in every way and demands a complete market reorganization. However, keeping in mind there are different types of battery cells (cylindrical, pouch, or prismatic) and various market players with specific needs, it is very challenging to satisfy them all in an optimal way. Still, both battery manufacturers, electric vehicle producers, and energy storage producers share similar demands in terms of battery cell packaging requirements for optimal protection and sustainable transportation solutions.
The number one priority for all three is safety. New technologies and better monitoring are making batteries a very safe way to store electricity. Still, in case of thermal runaway, there is a risk of an explosion. Therefore it is crucial for the cell and battery packaging to be designed in compliance with applicable regulations for its intended transport. This means that the packaging must be handled, packed, marked, stored, and transported according to international rules, as well as many domestic regulations. These are based on the UN recommendations on the transport of dangerous goods.
Customized solutions are equally important. With different battery types available on the market and various production standards, each packaging must meet individual customer demands. There is no one-size-fits-all option here. Assembly line limitation, for instance, is important to consider when choosing the right packaging material and design. Optimizing the flows of LiBs packaging simplifies the automation of the process of unloading the batteries from the truck to the warehouse and speeds up the production line. Also, the cleanliness standards of the battery production lines have a big influence on the customized packaging.
Last, but not least, let’s talk about sustainability. Using recycled materials for cell packaging is one way of ensuring less waste, reducing package weight, and decreasing the environmental footprint. It is crucial to remember that batteries have a high density and trucks are mostly maxed out by weight rather than volume. Hence a lower weight of the packaging allows for more batteries per truck. However, a new approach to circularity is to reuse the same packaging for transporting new batteries as many times as possible. This solution, known as the returnable packaging system, is nothing new to automotive Original Equipment Manufacturers (OEMs), however, it is a novelty for LiB producers. It wasn’t an option until now for long-destination transportation from China to Europe, but with the shift to regional production, it can be an attractive way to optimize costs and material use.
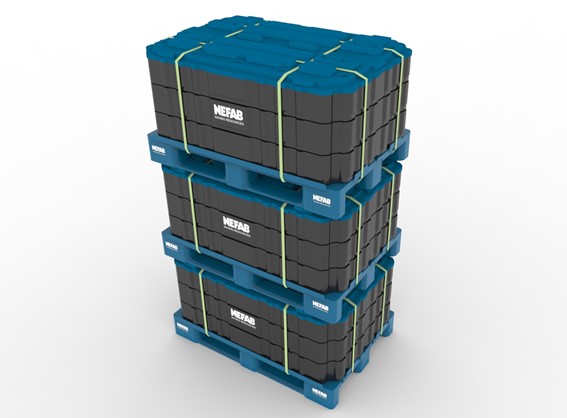
An UN-certified returnable packaging for LiB cells or batteries designed for automated handling.
Clean road ahead
LiBs power the lives of millions of people each day and have reshaped the modern world in many ways. They also have the potential to decarbonize transportation and help combat climate change. The energy storage revolution is unstoppable.
Transporting LiBs is a challenge and many market players have been desperately looking for safe and sustainable packaging as well as fully automated logistic solutions. Designing and creating sturdy yet light packaging, given all the safety precautions and production line limitations, is not an easy task. Fully developed and operating automated logistic solutions can be very costly to implement.
If you want to learn more, stay tuned as details of specific solutions for this unique market application will be unfolded in the next blog posts.
We save resources in supply chains, for a better tomorrow.
Want to learn more?
GET IN TOUCH
Contact us to learn more about our sustainable solutions.
LEARN MORE
GreenCALC
Nefab’s own certified calculator measures and quantifies financial and environmental savings in our solutions
Sustainable Solutions
Engineered packaging for sustainable supply chains
Sustainable Materials
Fiber-based packaging and raw materials